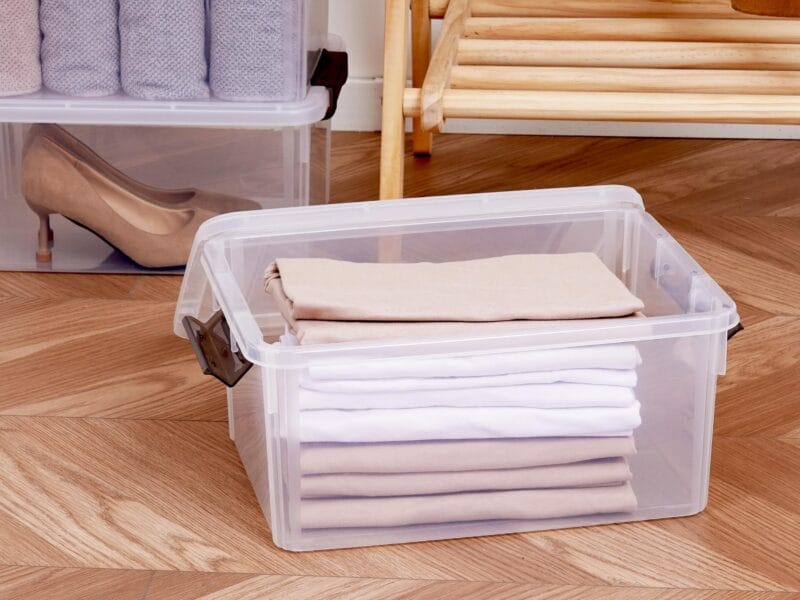
プラスチック収納ボックスの製造工程は、複数の重要な工程と専門的な技術を伴う複雑で繊細なプロセスである。この記事では LEBO は、当社のプラスチック製収納ボックスの製造工程と、その色がどのようにカスタマイズされているかをご紹介します。
プラスチック収納箱の製造工程
原材料の選択と準備
原材料の選択: プラスチック収納箱の主原料には、ポリプロピレン(PP)やポリエチレン(PE)などの熱可塑性プラスチックが含まれる。これらの素材は軽量で耐摩耗性、耐食性に優れ、加工が容易であるため、収納箱の製造に非常に適している。
原材料の着色とプロポーショニング: 製品の色とデザインの要求に応じて、プラスチック原料をトナー、エンジンオイル、その他の添加剤と一定の割合で混合し、ミキサーで均一に撹拌して着色顔料を作る。この工程により、プラスチック収納箱の最終的な色とデザインが確保される。
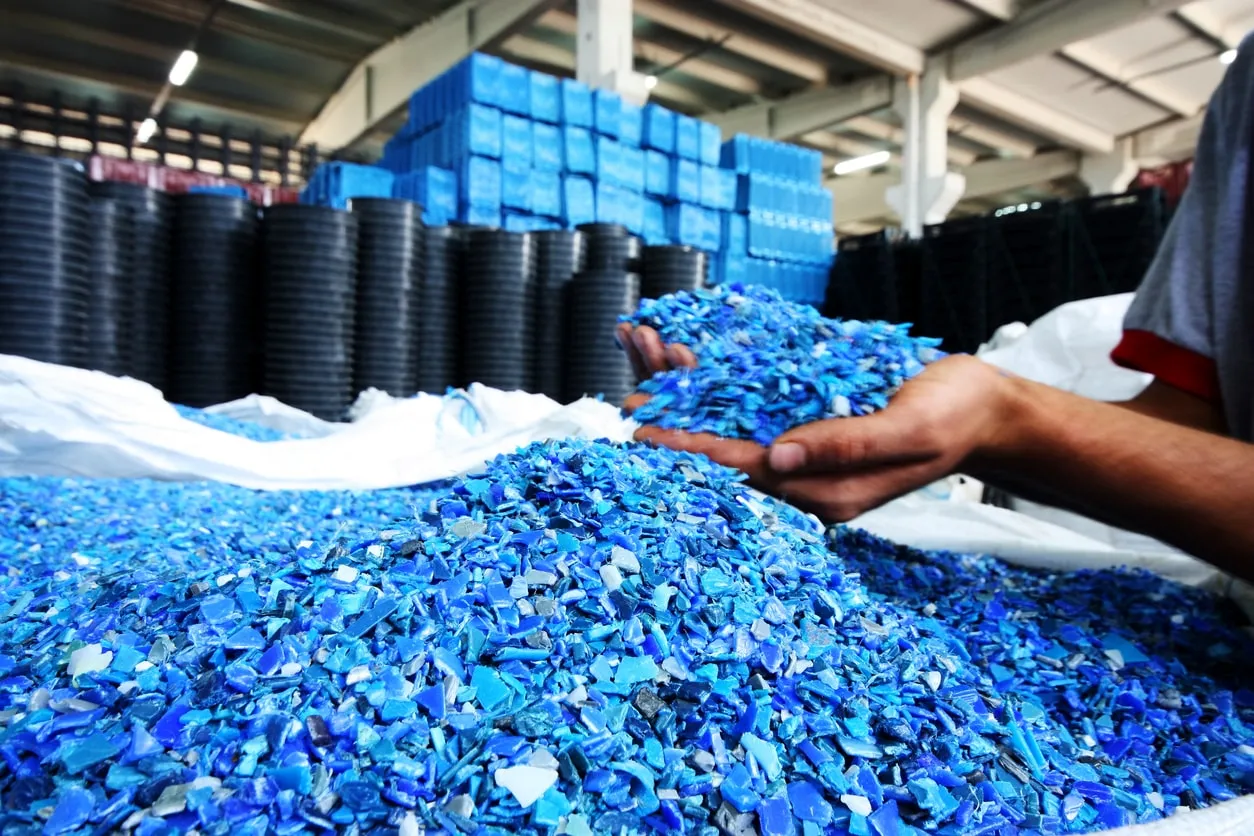
金型の設計と製造
金型設計: 金型はプラスチック収納箱の生産工程における重要なツールである。その設計は、収納容器のサイズ、構造、肉厚などの要素を考慮する必要があります。金型の設計は通常、専門的なCAD/CAMソフトウェアを使用して行われ、金型の精度と効率を確保します。
金型製造: 精密機械加工設備(CNC工作機械など)を使用して、設計図面に従って金型を製造する。金型が製造された後、それが生産要件を満たしていることを確認するために、厳格な検査と金型テストが必要です。
射出成形
射出成形機の準備: 準備したプラスチック原料を射出成形機のホッパーに入れ、射出成形機の温度、圧力などのパラメーターを設定する。
射出成形: 射出成形機は、溶融プラスチックを金型に注入し、冷却して収納箱の予備形状を形成する。射出成形工程では、製品の品質と寸法精度を確保するために、温度、圧力、時間などのパラメータを厳密に制御する必要があります。
脱型と後処理: 射出成形完了後、金型を開いて製品を取り出し、バリ取りやトリミングなどの後加工を行う。これらの工程を経ることで、プラスチック収納箱の外観品質と性能を向上させることができる。

表面処理
プラスチック収納箱の外観品質と耐久性を向上させるために、通常、表面処理が必要である。一般的な表面処理方法としては、帯電防止処理、紫外線均一処理などがあります。これらの処理は、材料自体の静的負荷を低減し、ほこりの吸収を防ぐことができます。同時に、プラスチック収納箱の色をより鮮やかにし、耐久性を向上させる。
組み立てとテスト
組み立て:プラスチック収納ボックスの各部品を組み立てて、収納ボックス製品を完成させる。組み立ての際、製品の安定性と耐久性を確保するため、部品のマッチングと気密性に注意を払う必要がある。
テスト:組み立てられた収納ボックスの外観検査、寸法測定、機能検査などの品質検査を行う。品質基準を満たした製品だけが次の工程に進むことができる。
梱包と配送
パッケージング: 認定プラスチック保管箱は、輸送や保管中の損傷から製品を保護するために包装されています。包装材料には通常、カートン、ビニール袋などが含まれます。
配達: 梱包後、プラスチック収納箱は販売拠点や倉庫に出荷され、販売されます。納品前には、製品の数量と品質が要件を満たしていることを確認するため、最終検査と棚卸しが必要です。
まとめると、プラスチック収納箱の製造工程は、原材料の選択、金型の設計と製造、射出成形、表面処理、組み立てとテスト、梱包と配送など、複数のリンクを含む複雑で繊細なプロセスである。製品の品質と性能が要件を満たすように、各リンクを厳密に制御し、チェックする必要があります。
プラスチック収納ボックスの色をカスタマイズするには?
ニーズを特定する
まず、カラーコード(PANTONEの色番号など)、色効果(つや消し、光沢など)、特殊な視覚効果(グラデーション、金属光沢など)の要求の有無など、顧客が要求するバルクプラスチック収納箱の色の具体的な要求を明確に理解する必要がある。
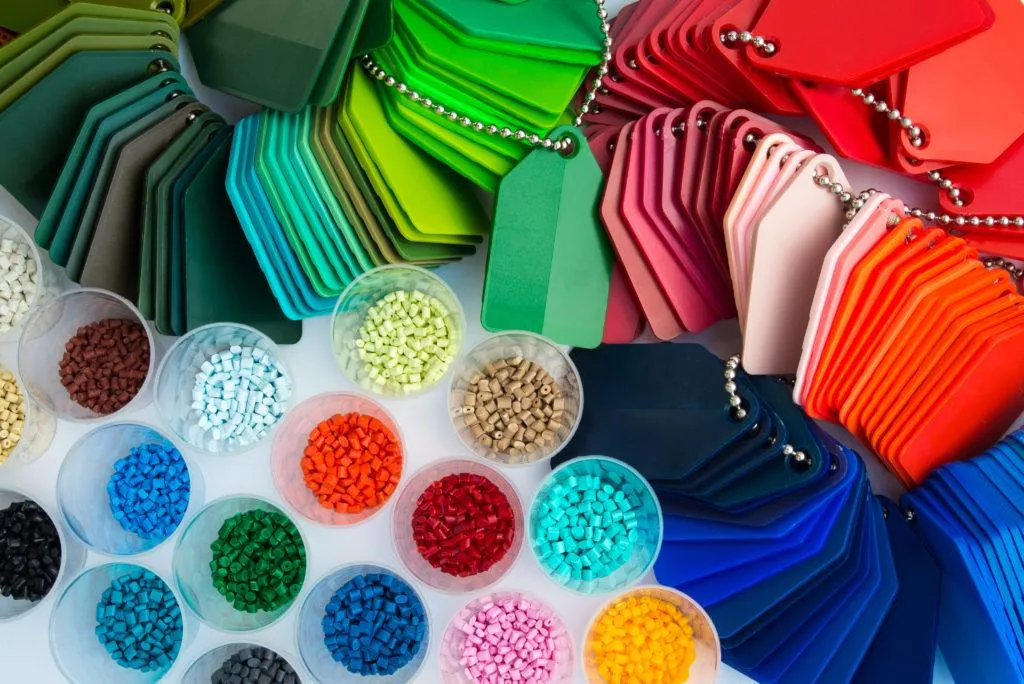
サンプル確認
設計計画:お客様のニーズに基づき、Leboのデザイナーが収納ボックスのデザイン案を作成します。色選びがお客様の期待に沿うよう、デザインプランは何度もお客様とコミュニケーションを取り、確認する必要があります。
カラーサンプル:デザインプランが最初に承認された後、Leboは色見本を作成したり、デザインレンダリングを提供したりして、お客様が色の実際の効果をより直感的に理解できるようにします。
原材料の準備
原材料の選択:設計計画で決定された色に応じて、適切なプラスチック原料を選択し、着色するために対応する色の粉末またはマスターバッチを追加します。原料の選択は、色の安定性、耐候性、耐摩耗性などの要素を考慮する必要がある。
原料着色:カラーパウダーまたはマスターバッチをプラスチック原料と一定の割合で混合し、着色効果が一貫しており、必要なプラスチック収納ボックスのデザインに合うようにします。
射出成形
金型の準備: 射出成形用金型がきれいで破損していないことを確認し、設計要件に従って温度や圧力などの金型パラメータを調整する。
射出成形: 着色されたプラスチック原料は金型に射出され、冷却後にプラスチック収納箱の初期形状が形成される。射出成形工程では、製品の色と品質を確保するために、温度、圧力、時間などのパラメータを厳密に制御する必要があります。
色の検査と調整
予備検査: 射出成形された収納箱の予備的な色検査を行い、色が均一で一貫しているかをチェックし、設計要件と比較する。
調整と最適化: もし色彩が逸脱したり、要求を満たさない場合、時間内に原料比率、射出成形パラメーターなどを調整し、色彩効果が顧客の満足を満たすまで何回も調整する必要がある。
その後の加工と包装
バリ取りとトリミング: 射出成形された収納箱にバリ取りやトリミングなどの後加工を施し、製品の外観品質を向上させる。
カラープロテクト: 必要に応じて、プラスチック収納ボックスは表面処理(UV均一処理など)を施し、色の耐久性と光沢を高めることができる。
梱包と配送: その後のすべての処理が完了した後、バルクプラスチック保管箱は梱包され、配送の準備が整う。梱包工程では、製品の色を損傷から守る必要がある。
顧客確認とフィードバック
サンプル確認: 大量生産の前に、通常、顧客の確認のために少数のサンプルが作られる。顧客はサンプルの色、品質などを総合的に検査し、フィードバックする必要がある。
大量生産: 顧客がサンプルに間違いがないことを確認した後、Leboは大量生産を実施する。各バッチの製品の色が一貫しており、設計要件を満たしていることを確認するために、生産プロセスでは依然として色の品質を厳密に制御する必要があります。
以上の手順により、カスタマイズされたプラスチック収納ボックスが顧客の期待に応える色合いと、顧客のニーズを満たす高い品質レベルを維持することが保証される。
プラスチック収納ボックスのサプライヤーとしてLEBOをお選びください
高品質、耐久性、デザイン性に優れたプラスチック収納箱を大量にお探しなら、 LEBO は間違いなくあなたの優先サプライヤーです。30年以上の経験を持つプラスチック収納箱メーカーとして、様々なシーンに合わせたサイズ、色、機能の収納箱など、多様な製品ラインを提供しています。
私たちが生産するプラスチック収納箱は高品質で、耐衝撃性、耐久性に優れ、洗浄が簡単で、日常使用における様々な課題に耐えることができます。また、弊社が生産するプラスチック収納箱は、環境に優しい材料で作られ、安全で無害であり、消費者は安心して使用することができます。
私たちは、お客様との長期ビジネスを確立されています。私達のプロダクトの何れかのモデルに興味がある場合は、お問い合わせは、自由にしてくださいを参照してください。お問い合わせは歓迎します。 ここをクリック をクリックして、プラスチック収納ボックスをご覧ください。