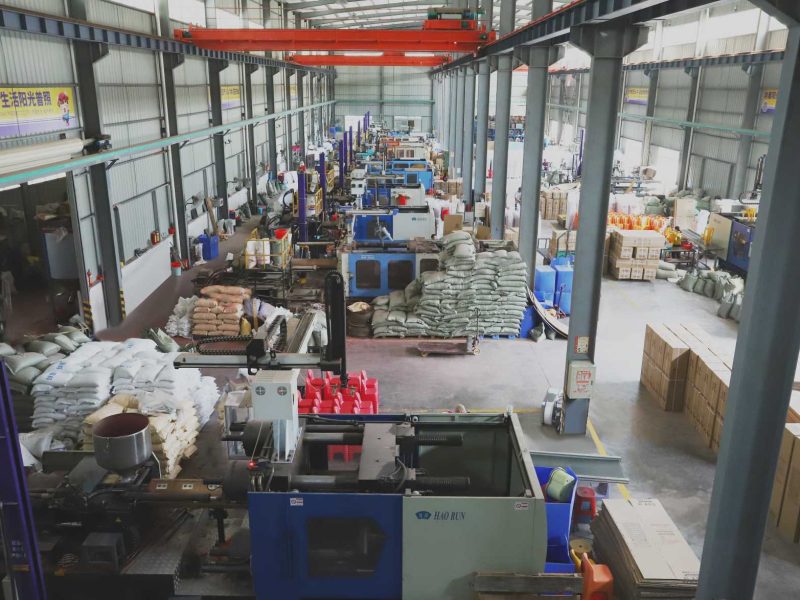
In the ever-changing daily consumer goods market, plasticware products occupy a core position in the B2B field with their lightweight, durable, affordable and versatile characteristics. Whether it is plastic food containers in home kitchens, document storage boxes in offices, or a wide range of commodity packaging in supermarkets, plasticware products have become an important bridge connecting manufacturers and consumers with their unique advantages. They not only enrich daily life, but also play an irreplaceable role in improving the convenience of life and promoting innovation in environmentally friendly materials.
The purpose of this blog is to reveal how our one-stop customized plasticware solution can greatly simplify the procurement process for B2B customers through technological innovation and process optimization, enhance the smoothness of cooperation, and thus improve the user experience of end users through a meticulous deconstruction of the entire process from creative incubation, design proofing, large-scale manufacturing to seamless delivery.
As an experienced manufacturer of plastic food containers, home storage containers, lunch boxes, and plastic homewares, LEBO Plastic hopes that through this in-depth analysis, we will not only deepen the industry’s understanding and trust in our service model but also encourage more partners to join us to explore the infinite innovation possibilities of the daily plasticware products industry and work together to create a new era of more intelligent, green and humanized daily necessities.
The Necessity of One-stop Customized Plasticware Solutions
Faced with the diversified and personalized needs of the daily plasticware products market, traditional procurement and supply models have gradually shown their limitations. At this time, “one-stop customized plasticware product solutions” as an innovative force highlight its unique value in improving supply chain efficiency, precise cost control and deepening customized plasticware services:
1. Efficiency optimization: One-stop customized plasticware solutions integrate the entire chain of services from design, production to logistics, eliminate the cumbersomeness of the intermediate links, achieve rapid response to market changes, shorten the time from product creativity to shelf, and help customers seize business opportunities.
2. Cost calculation: Through large-scale production and efficient allocation of resources, one-stop customized plasticware service can effectively reduce costs while ensuring product quality, provide B2B partners with the most competitive price plan, and jointly resist market fluctuations.
3. In-depth customization: In view of the wide range of uses and aesthetic preferences of daily plasticware products, we provide a full range of customized services from material selection to product design to ensure that each product can accurately match the target market and consumer needs, and enhance brand differentiation competitiveness.
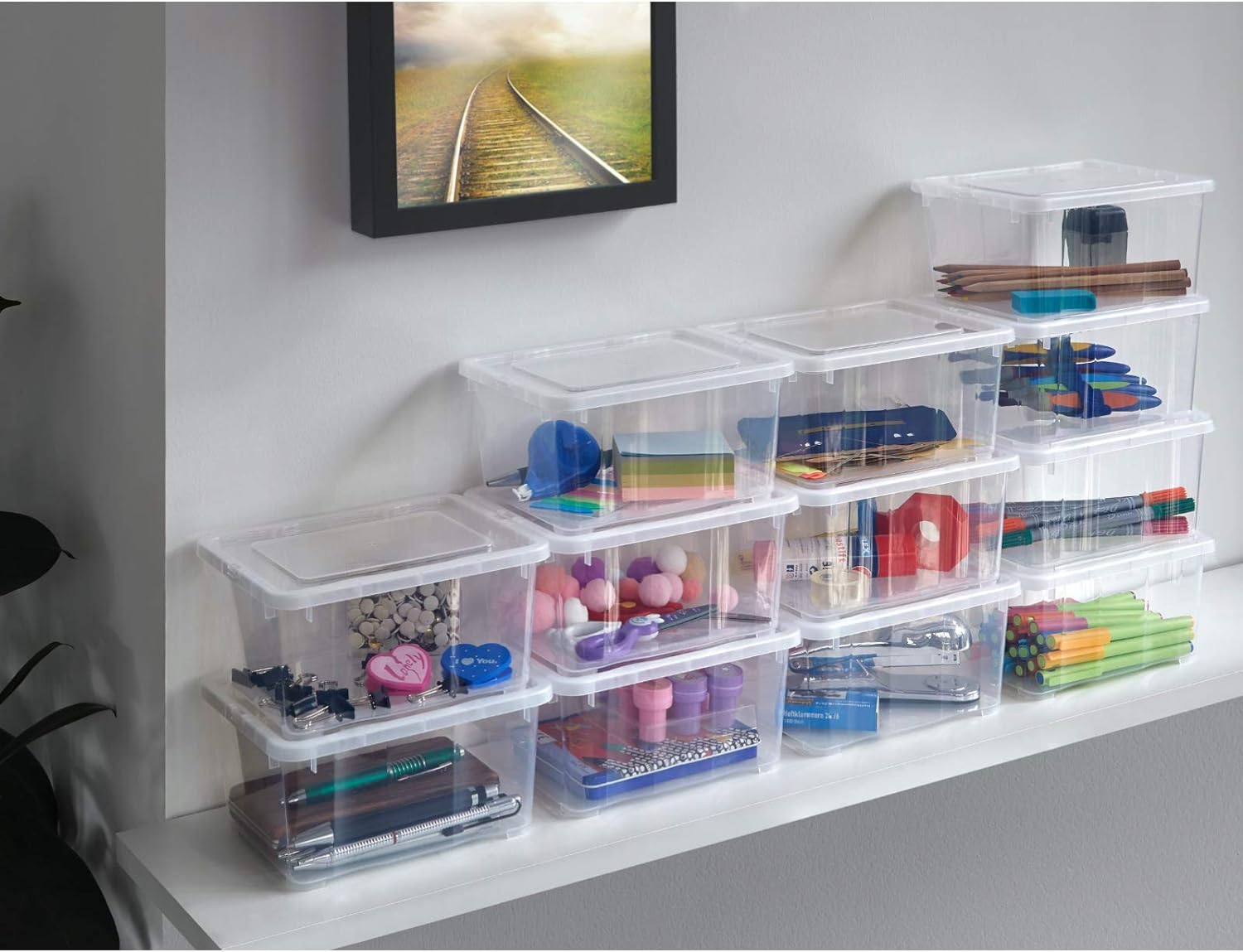
Demand Analysis and Preliminary Communication
In the customized plasticware products service process, the first step is to deeply understand and accurately match customer needs. This is not only the key to the success of the project, but also the cornerstone of creating customer-satisfied products. The following three links constitute our meticulous demand analysis and preliminary communication stage:
In-depth demand interview: accurately lock the core of demand
Application scenario analysis: We will discuss with customers in depth the expected use environment of the product, whether it is a home kitchen, office, outdoor travel or commercial retail. Clear use scenarios will help us make reasonable choices in terms of material temperature resistance, durability, and aesthetics.
Clear functional requirements: For the specific functions that the product needs to have, such as sealing, drop resistance, easy cleaning, microwave safety, etc., we will confirm them one by one to ensure that the design and production can meet the actual use needs.
Expected goal setting: Understand the customer’s market positioning, target consumer groups and expected effects of the product, so as to help us incorporate brand concepts and market orientation in the early stage of design.
Market trend insight: forward-looking perspective leads innovation
Trend analysis report: Our market research team will regularly analyze the latest trends in daily plastic products, covering environmentally friendly materials, design styles, technological innovations, etc., to provide customers with forward-looking customized plasticware suggestions.
Personalization and differentiation: In combination with industry trends, we suggest how to make products stand out in the fiercely competitive market through customized plasticware design, such as introducing degradable materials, intelligent functions or unique appearance design.
Cost-effectiveness optimization: the art of cost-effectiveness
Budget assessment: fully understand the customer’s budget range to ensure that the design plan meets cost expectations without sacrificing necessary performance indicators.
Performance and cost balance: by selecting appropriate material grades, optimizing design structures, and large-scale production, we can control costs to the maximum extent while ensuring product performance and providing the most cost-effective customized plasticware solution.
Return on investment analysis: For long-term cooperative customers, we will also provide a return on investment forecasts to help customers foresee the economic benefits of the product life cycle and ensure the scientific and forward-looking nature of decision-making.
Through this series of in-depth communication and analysis, we can not only accurately capture customer needs, but also provide customers with forward-looking innovative suggestions, and finally jointly develop customized plasticware product solutions that meet market trends and cost-effectiveness requirements.
Product Design and Prototype Development
After establishing a detailed needs analysis, we enter the product design and prototype development stage, which is a process of turning ideas into reality and continuously iterating and optimizing. The following three steps ensure that we can efficiently and accurately transform customer visions into high-quality customized plasticware product prototypes.
Professional strength of the design team
Experienced designers: Our design team brings together professionals with many years of industry experience. They are proficient in perfectly integrating practicality and aesthetics to ensure that the design is both ergonomic and market-appealing.
Diversified skills: Team members include industrial designers, material experts, and structural engineers. Their interdisciplinary background ensures full consideration from concept to detail, whether it is complex structural design or the application of new materials.
Innovative thinking leadership: Encouraging innovation is our core culture. The design team constantly explores cutting-edge design trends and technologies, such as smart sensing, environmentally friendly material applications, etc., to inject innovative souls into products.
Efficient CAD design and 3D printing technology
CAD design software: Using CAD software, quickly build accurate three-dimensional models, which is convenient for reviewing product design from multiple angles and discovering and solving potential structural problems in advance.
3D printed prototype: With the help of 3D printing technology, we can transform the design drawings into physical prototypes in a short time, allowing customers to intuitively experience the appearance, size and feel of the customized plasticware product, and accelerate the product verification process.
Rapid iteration: Through the combination of CAD and 3D printing, we can quickly adjust the design based on feedback and achieve multiple iterations until the best design effect of customized plastic products is achieved.
Deep customer participation to ensure design satisfaction
Open communication channels: We establish a close customer communication mechanism to ensure that customers participate in the design process throughout the customized plasticware process. From the first draft of the sketch to the prototype review, customer feedback will be solicited and absorbed at each key node.
Feedback loop: Set up a fast feedback mechanism to collect customer opinions on the customized plasticware product design prototype. Whether it is improvement suggestions on function, aesthetics or user experience, we will respond in time and make necessary adjustments.
Design confirmation: After multiple rounds of modification and improvement, the final customized plasticware product design must be fully recognized by the customer to ensure that the developed prototype fully meets or exceeds the customer’s original expectations.
Through this series of carefully designed and closely coordinated processes, we ensure that each customized plasticware product project can accurately meet market demand and customer specific requirements while maintaining innovation and practicality, laying a solid foundation for subsequent production and manufacturing.
Material selection and sample making
After ensuring that the design is both functional and attractive, we enter the crucial material selection and sample making stage, which is a key step in determining product quality and environmental performance. We are committed to building a bridge between material science and practical applications to ensure that every daily plastic product can reflect environmental responsibility and durability.
Integration of material science and environmental trends
Safety first: We strictly abide by international safety standards to ensure that the selected materials are non-toxic and harmless, suitable for food contact or children’s products, and ensure user safety.
Durability considerations: Comprehensively consider the physical properties of the material such as strength, toughness, and temperature resistance to ensure that the product is durable in daily use, reduce the frequency of replacement, and indirectly promote sustainable development.
Environmental trend guidance: Actively respond to the global environmental protection call, give priority to recyclable or biodegradable materials, reduce the impact on the environment, and meet the market’s preference for green products.
Sample making: quality and efficiency are equally important
Strict quality control: The sample making process follows the ISO quality management system, and every step from raw material inspection to molding processing is strictly monitored to ensure reliable sample quality.
Fast sample service: using advanced mold technology and efficient production process, shortening the sample production cycle, quickly responding to customer needs, and accelerating the transformation process from design to market.
Detail processing: focusing on the surface treatment, color matching and texture of the customized plasticware sample, striving to make the sample highly consistent with the design draft, and providing customers with intuitive and real visual and tactile experience.
Sample testing and feedback loop with customer participation
Actual application testing: we encourage customers to test samples in real-use scenarios, evaluate their functionality, durability and user experience, and collect first-hand feedback information.
Multi-dimensional feedback collection: We not only pay attention to customer opinions, but also consider the feedback of end users to fully understand the acceptance of products in the market.
Continuous optimization: based on test feedback, our design and production teams respond quickly and make necessary adjustments to materials, structures or production processes of our customized plasticware products until the samples fully meet or exceed customer expectations.
Through this rigorous and flexible material selection and sample production process, we not only ensure the high quality and environmental protection of customized plasticware products, but also through close cooperation with customers, continuously optimize products to make them closer to market demand, and finally create high-quality daily plastic products that are both safe and reliable and in line with environmental protection trends.
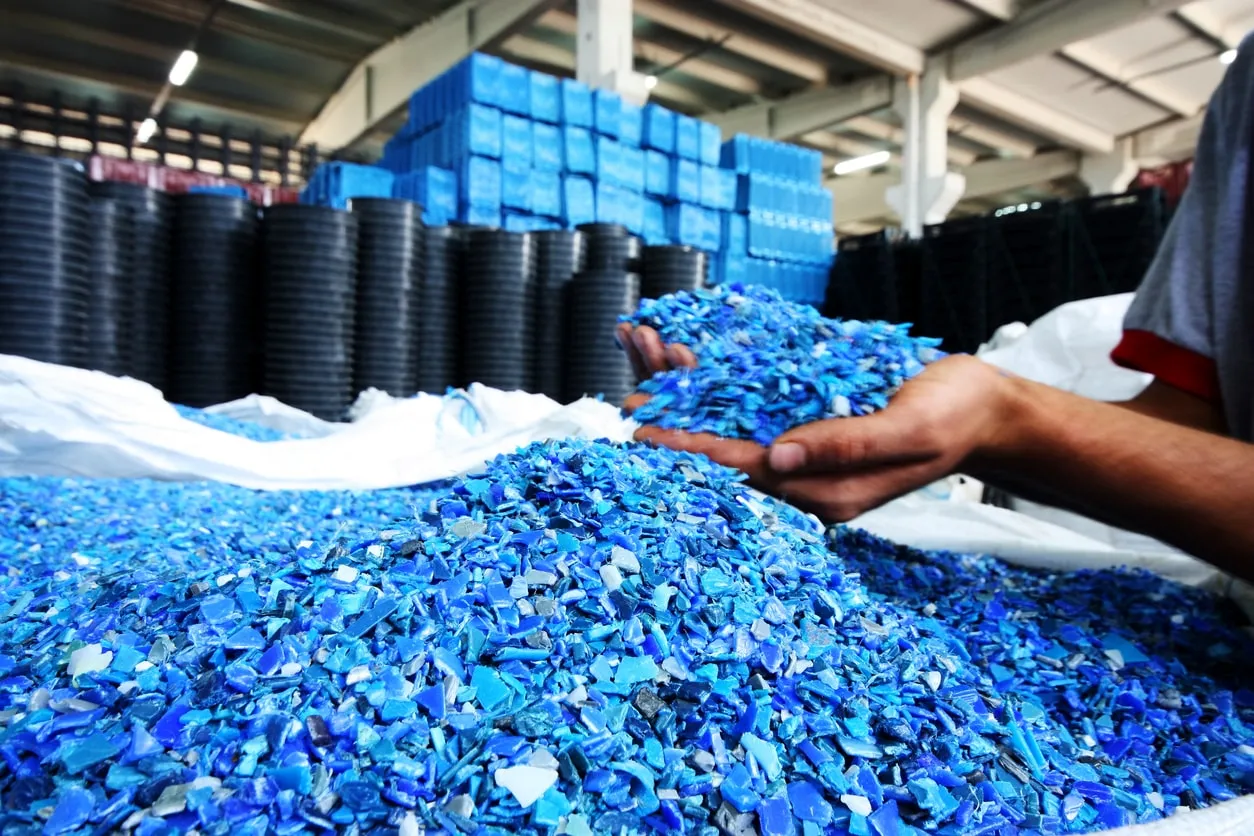
Preparation for mass production
Before entering mass production, we carefully prepare to ensure the efficiency and flexibility of the production line to meet various order requirements.
Production line overview: Our production facilities are equipped with advanced automation equipment, such as injection molding machines, blow molding machines, etc., which can achieve high-precision and high-speed production. Strong production capacity ensures a quick response to the market. At the same time, a comprehensive quality management system runs through the entire production process to ensure the quality of each process.
Process optimization: Adopting the principle of lean production, reducing unnecessary steps through process reengineering, eliminating waste, and improving overall customized plasticware production efficiency. The intelligent scheduling system ensures the efficient flow of raw materials to finished products and shortens the production cycle.
Order management and production planning: Establish a flexible order management system to respond quickly to both small-batch customization and large-volume orders. The production plan is flexibly adjusted according to customer needs to ensure on-time and in-quantity delivery.
Quality Control and Testing
Quality is our constant pursuit, ensuring that every product can meet the highest standards.
Quality Control System: LEBO Plastic implements strict quality control standards, and has strict testing procedures at every step from raw material storage to finished product delivery.
Third-party testing and certification: Products are tested for performance and safety by third-party laboratories to ensure compliance with international safety and environmental regulations.
Continuous Improvement Mechanism: Based on production data and customer feedback, we continuously optimize production processes and product design to continuously improve product quality and performance.
Packaging and Logistics Solutions
Safe and environmentally friendly packaging and efficient logistics services ensure that products are delivered to customers intact.
Customized plasticware packaging design: Provide environmentally friendly and highly protective customized packaging to protect the integrity of the product during transportation and enhance the brand image.
Environmentally friendly packaging materials: Use recyclable or biodegradable materials to respond to the trend of sustainable development and reduce environmental burden.
Global logistics network: Relying on mature logistics partners, we provide fast and safe global distribution solutions, full tracking services, and ensure on-time delivery.
After-sales service and continuous support
We firmly believe that high-quality after-sales service is the cornerstone of establishing a long-term cooperative relationship.
Customer satisfaction survey: Regularly visit customers, collect usage feedback, and continuously optimize services.
Product upgrade and iteration service: Provide product upgrade services according to market changes and customer needs, grow together with customers, and establish long-term cooperative relationships.
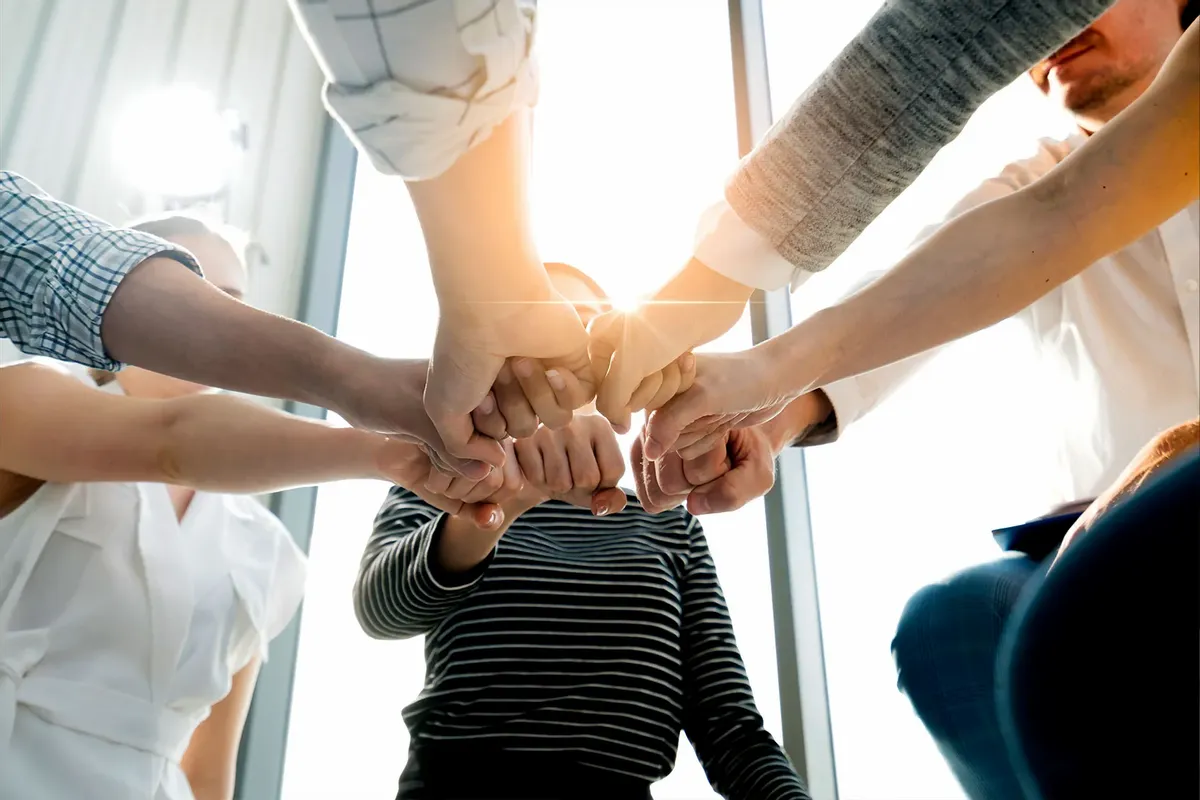
Conclusion
The core value of a one-stop customized plasticware product solution is to simplify the entire process from design to market for customers, accelerate product time to market, and strengthen customers’ market competitiveness through efficient quality control, environmentally friendly packaging and logistics solutions, and thoughtful after-sales service. LEBO Plastic attaches great importance to the flexibility and customization capabilities of cooperation, and is committed to meeting the diverse needs of every B2B customer. We sincerely invite partners from all industries to join hands with us to start a journey of cooperation and create a win-win future!